مشکلات رایج در تولید سیمان و راه حل ها
مشکلات رایج در تولید سیمان و راهکارهای عملی
سیمان به عنوان یکی از حیاتی ترین مصالح ساختمانی نقش بسزایی در توسعه زیرساخت ها و پروژه های عمرانی ایفا می کند. فرآیند تولید این ماده مسیری پیچیده و چند مرحله ای است که از لحظه استخراج مواد اولیه از دل زمین آغاز شده و تا بسته بندی محصول نهایی ادامه می یابد.
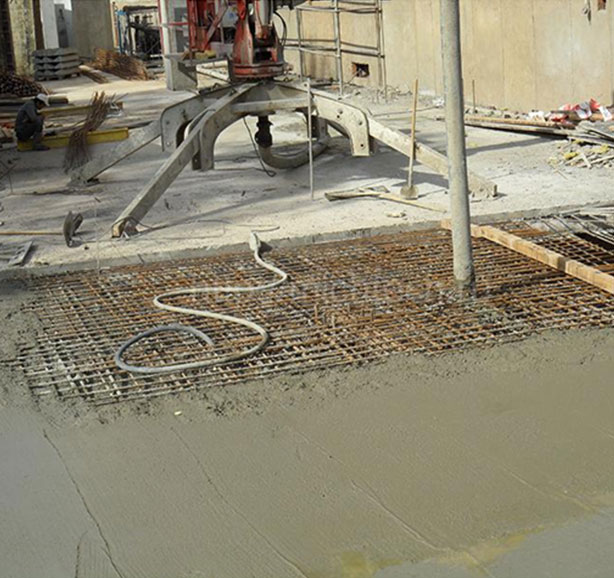
این زنجیره تولید شامل مراحل کلیدی مانند استخراج آماده سازی مواد پخت کلینکر در کوره های دوار با دمای بسیار بالا و در نهایت آسیاب کلینکر به همراه افزودنی ها برای تولید سیمان نهایی است. در هر گام از این فرآیند صنعتی پیچیده چالش ها و مشکلاتی بالقوه وجود دارند که می توانند بر کیفیت محصول راندمان تولید هزینه ها و حتی مسائل زیست محیطی تأثیرگذار باشند.
شناخت دقیق این مشکلات رایج و آگاهی از راهکارهای عملی و مؤثر برای مقابله با آن ها نه تنها برای متخصصان و دست اندرکاران صنعت سیمان ضروری است بلکه برای تضمین پایداری و بهره وری خطوط تولید افزایش کیفیت محصول نهایی و کاهش اثرات زیست محیطی این صنعت اهمیت حیاتی دارد. این مقاله با هدف بررسی جامع این چالش ها و ارائه راه حل های مبتنی بر دانش روز و تجربیات عملی در صنعت سیمان تدوین شده است. قیمت سیمان اصفهان در الومتریال ببینید و در صورتی که به روز نباشد باید تماس بگیرید و قیمت روز را دریافت کنید.
مقدمه ای بر فرآیند تولید سیمان
تولید سیمان پرتلند که رایج ترین نوع سیمان است فرآیندی صنعتی با فناوری بالا محسوب می شود. این فرآیند به طور کلی به چهار مرحله اصلی تقسیم می شود: استخراج و خردایش مواد اولیه آماده سازی خوراک کوره (شامل آسیاب و اختلاط) پخت کلینکر و آسیاب نهایی سیمان. هر مرحله دارای پیچیدگی ها و نیازمندی های خاص خود است.
مواد اولیه اصلی شامل سنگ آهک (منبع اصلی اکسید کلسیم) و مواد رسی یا شیل (تأمین کننده سیلیس آلومینا و اکسید آهن) هستند. این مواد پس از استخراج تحت فرآیندهای فیزیکی و شیمیایی قرار می گیرند تا در نهایت به سیمان با خواص مورد نظر تبدیل شوند. کنترل دقیق پارامترهای فرآیندی در هر مرحله کلید دستیابی به محصولی با کیفیت و تولیدی پایدار و مقرون به صرفه است.
مشکلات رایج در مرحله استخراج مواد اولیه
مرحله استخراج مواد اولیه به عنوان نقطه آغازین زنجیره تولید سیمان اهمیت بنیادینی دارد. کیفیت کمیت و ترکیب شیمیایی سنگ آهک خاک رس مارل و دیگر افزودنی های طبیعی که از معادن استخراج می شوند مستقیماً بر کل فرآیند تولید و کیفیت سیمان نهایی تأثیر می گذارند. با این حال این مرحله با چالش های متعددی روبروست.
یکی از اصلی ترین مشکلات تنوع و نوسان در کیفیت مواد استخراج شده است. رگه های معدنی ممکن است دارای ترکیب شیمیایی متفاوتی باشند یا حاوی ناخالصی های نامطلوب باشند. این ناخالصی ها می توانند شامل منیزیم اکسید بیش از حد قلیاها کلریدها یا سولفات ها باشند که بر خواص سیمان نهایی مانند مقاومت گیرش و پایداری حجمی اثر منفی می گذارند. بنابراین نیاز به کنترل کیفیت دقیق در محل استخراج و تفکیک مواد بر اساس کیفیت امری ضروری است.
مشکل دیگر آلودگی مواد معدنی است. این آلودگی می تواند ناشی از ورود خاک سطحی مواد آلی یا مواد معدنی ناخواسته در فرآیند حفاری و استخراج باشد. آلودگی ها نه تنها ترکیب شیمیایی خوراک کوره را بر هم می زنند بلکه می توانند باعث مشکلاتی در فرآیندهای بعدی مانند آسیاب یا پخت شوند. به عنوان مثال وجود مقادیر زیاد مواد آلی می تواند باعث ایجاد مشکلات در کوره و افزایش مصرف سوخت شود.
مسائل مربوط به حمل و نقل مواد استخراج شده نیز چالش برانگیز است. معادن معمولاً در فواصل دور از کارخانه قرار دارند و حمل و نقل مواد حجیم نیازمند زیرساخت های مناسب تجهیزات حمل و نقل سنگین و مدیریت لجستیک کارآمد است. هزینه های بالای حمل و نقل تأخیر در رسیدن مواد و مشکلات ناشی از شرایط آب و هوایی می توانند بر پایداری و هزینه تولید تأثیر بگذارند.
علاوه بر این فرآیندهای انفجار و حفاری در معادن نیز چالش های خاص خود را دارند. انتخاب روش مناسب انفجار برای خردایش بهینه سنگ کنترل ارتعاشات و گرد و غبار ناشی از انفجار برای حفظ محیط زیست و ایمنی و همچنین پایداری دیواره های معدن نیازمند دانش فنی و برنامه ریزی دقیق است. تولید دانه بندی نامناسب پس از انفجار می تواند بر راندمان خردایش اولیه تأثیر بگذارد.
آلودگی مواد اولیه
آلودگی مواد اولیه یکی از جدی ترین چالش ها در ابتدای فرآیند تولید سیمان است. این آلاینده ها می توانند به صورت ذاتی در رگه های معدنی وجود داشته باشند یا در حین فرآیندهای استخراج بارگیری حمل و نقل و دپو به مواد اضافه شوند. مهمترین آلاینده ها شامل موارد زیر هستند:
- مواد آلی: می توانند در خاک رس یا سنگ آهک وجود داشته باشند و در کوره باعث مشکلات احتراق و افزایش مصرف سوخت شوند.
- قلیاها (سدیم و پتاسیم اکسید): مقادیر بالای آن ها می تواند باعث تشکیل حلقه ها و پوشش های ناخواسته در کوره افزایش مصرف سوخت و تأثیر منفی بر خواص سیمان مانند مقاومت در برابر حمله سولفات ها و واکنش قلیایی سنگدانه شوند.
- کلریدها: می توانند باعث خوردگی تجهیزات و تشکیل رسوبات در سیستم پیش گرمکن کوره شوند.
- منیزیم اکسید (MgO): مقادیر بیش از حد آن در سنگ آهک می تواند باعث انبساط نامطلوب و کاهش پایداری حجمی سیمان سخت شده شود.
- سولفات ها: مانند گچ طبیعی اضافی یا پیریت می توانند بر فرآیند پخت و خواص سیمان تأثیر بگذارند.
برای جلوگیری از این مشکلات انجام آزمایش های دوره ای و منظم بر روی نمونه های استخراج شده از نقاط مختلف معدن قبل از ارسال به کارخانه ضروری است. استفاده از تکنیک های نمونه برداری آماری و آنالیز شیمیایی سریع (مانند آنالیزورهای XRF پرتابل در محل معدن) می تواند به شناسایی زودهنگام رگه های آلوده کمک کند.
در مواردی که آلودگی قابل توجه است ممکن است نیاز به استفاده از روش های جداسازی فیزیکی یا شیمیایی باشد هرچند این روش ها معمولاً پرهزینه هستند. بهترین راهکار شناسایی و تفکیک مناطق با کیفیت پایین در معدن و مدیریت دقیق فرآیند استخراج برای به حداقل رساندن ورود مواد آلوده به خط تولید است. همچنین برنامه ریزی دقیق برای ترکیب مواد اولیه از منابع مختلف (Blending) می تواند به یکنواخت کردن ترکیب خوراک کوره و کاهش تأثیر نوسانات کیفیت کمک کند. جهت مشاهده روند تولید سیمان بهتر است به ویدوئوهای یوتیوپ مراجعه کنید.
مشکلات در مرحله آماده سازی مواد
مرحله آماده سازی مواد شامل خردایش اولیه خشک کردن (در صورت نیاز) و آسیاب مواد اولیه برای رسیدن به دانه بندی مناسب و اختلاط آن ها برای تشکیل خوراک کوره (Raw Meal) است. این مرحله نقش حیاتی در تأمین خوراکی با ترکیب شیمیایی و فیزیکی یکنواخت برای کوره دارد. مشکلات این مرحله می توانند به طور مستقیم بر راندمان کوره و کیفیت کلینکر تأثیر بگذارند.
یکی از مشکلات اصلی در این مرحله استهلاک بالای تجهیزات خردایش و آسیاب است. مواد اولیه سیمان به ویژه سنگ آهک و سیلیس بسیار ساینده هستند. این سایش باعث فرسودگی سریع قطعات داخلی سنگ شکن ها آسیاب ها (مانند لاینرها و گلوله ها در آسیاب گلوله ای یا غلطک ها و سگمنت ها در آسیاب عمودی) و تجهیزات حمل و نقل مانند نوار نقاله ها می شود. استهلاک بالا منجر به کاهش راندمان نیاز به توقف های مکرر برای تعمیر و نگهداری و هزینه های بالای قطعات یدکی می شود.
مصرف بالای انرژی نیز یک چالش بزرگ در مرحله آماده سازی است. فرآیندهای خردایش و آسیاب به ویژه آسیاب مواد اولیه نیازمند انرژی الکتریکی قابل توجهی هستند. بهینه سازی فرآیند آسیاب استفاده از آسیاب های با راندمان بالاتر (مانند آسیاب های غلطکی عمودی یا VRM) به جای آسیاب های گلوله ای سنتی در ظرفیت های بالا و کنترل دقیق دانه بندی محصول می تواند به کاهش مصرف انرژی کمک کند.
تولید گرد و غبار یکی دیگر از مسائل مهم در این مرحله است. فرآیندهای خردایش و آسیاب حجم زیادی گرد و غبار تولید می کنند که نه تنها مشکلات زیست محیطی و بهداشتی ایجاد می کند بلکه باعث اتلاف مواد اولیه و کاهش راندمان تجهیزات می شود. استفاده از سیستم های جمع آوری گرد و غبار مؤثر مانند فیلترهای کیسه ای و الکترواستاتیکی در نقاط انتقال مواد و خروجی آسیاب ها برای کنترل انتشار گرد و غبار ضروری است.
گرفتگی آسیاب ها
گرفتگی در آسیاب های مواد اولیه به ویژه در آسیاب های گلوله ای یا آسیاب های عمودی که مواد مرطوب را پردازش می کنند یکی از مشکلات رایج و مختل کننده است. این گرفتگی معمولاً ناشی از وجود رطوبت بیش از حد در مواد اولیه یا وجود ذرات بزرگ و چسبنده است که باعث چسبیدن مواد به لاینرها گلوله ها یا غلطک ها و دیواره های آسیاب می شود.
هنگامی که مواد به دیواره ها یا اجزای داخلی آسیاب می چسبند فضای داخلی آسیاب کاهش می یابد حرکت مواد و گلوله ها (یا غلطک ها) مختل می شود و راندمان آسیاب به شدت افت می کند. در موارد شدید گرفتگی می تواند منجر به توقف کامل آسیاب و در نتیجه توقف خط تولید شود. پاکسازی گرفتگی ها معمولاً نیازمند توقف فرآیند و صرف زمان و نیروی کار زیادی است.
راهکارهای اصلی برای جلوگیری از گرفتگی آسیاب ها عبارتند از:
- خشک کردن مواد اولیه: اگر مواد اولیه دارای رطوبت بالایی هستند استفاده از سیستم های پیش خشک کن قبل از ورود به آسیاب ضروری است. این سیستم ها می توانند از گازهای داغ خروجی کوره یا کوره جداگانه برای کاهش رطوبت استفاده کنند.
- غربال کردن مواد اولیه: حذف ذرات بسیار بزرگ یا ناخالصی های چسبنده قبل از ورود به آسیاب می تواند از گرفتگی جلوگیری کند. استفاده از سرندهای لرزان یا تجهیزات مشابه در مسیر انتقال مواد اولیه توصیه می شود.
- استفاده از افزودنی های ضد گرفتگی: در برخی موارد افزودن مقادیر کمی از مواد ضد گرفتگی به خوراک آسیاب می تواند به کاهش چسبندگی مواد کمک کند.
- بهینه سازی پارامترهای آسیاب: تنظیم سرعت چرخش آسیاب میزان پرشدگی گلوله ها (در آسیاب گلوله ای) یا فشار غلطک ها (در آسیاب عمودی) و دبی هوای عبوری (در آسیاب های بادی) می تواند بر جریان مواد در داخل آسیاب و کاهش تمایل به گرفتگی تأثیر بگذارد.
مشکلات مربوط به پخت کلینکر
مرحله پخت کلینکر در کوره دوار قلب فرآیند تولید سیمان است. در این مرحله خوراک آسیاب شده مواد اولیه در دماهای بسیار بالا (حدود 1450 درجه سانتی گراد) پخته می شود تا کلینکر ماده اصلی سازنده سیمان تشکیل شود. این مرحله شامل واکنش های شیمیایی پیچیده ای است که منجر به تشکیل فازهای کلینکر (C3S, C2S, C3A, C4AF) می شود. مشکلات در این مرحله به شدت بر کیفیت کلینکر و سیمان نهایی مصرف انرژی و مسائل زیست محیطی تأثیر می گذارند.
یکی از مشکلات رایج تشکیل حلقه های کلینکر (Rings) و پوشش های ناخواسته (Coatings) در داخل کوره است. این پدیده ها زمانی رخ می دهند که مواد مذاب یا نیمه مذاب به دیواره داخلی کوره چسبیده و به مرور زمان لایه های ضخیمی را تشکیل می دهند. تشکیل حلقه ها می تواند باعث کاهش قطر داخلی کوره اختلال در جریان مواد و گازها کاهش ظرفیت تولید و حتی آسیب به لاینینگ نسوز کوره شود. پوشش ها نیز می توانند بر انتقال حرارت و راندمان پخت تأثیر منفی بگذارند.
مصرف بالای سوخت یکی دیگر از چالش های بزرگ در مرحله پخت است. کوره دوار نیازمند مقادیر عظیمی انرژی حرارتی برای رسیدن به دمای پخت کلینکر است. راندمان حرارتی کوره به عوامل متعددی بستگی دارد از جمله نوع سوخت مورد استفاده (گاز طبیعی مازوت زغال سنگ سوخت های جایگزین) طراحی کوره و سیستم پیش گرمکن کیفیت عایق بندی و کنترل دقیق فرآیند احتراق. بهینه سازی مصرف سوخت نه تنها هزینه ها را کاهش می دهد بلکه انتشار گازهای گلخانه ای را نیز محدود می کند.
آلودگی هوا ناشی از انتشار گازهای خروجی کوره به ویژه اکسیدهای نیتروژن (NOx) اکسیدهای گوگرد (SOx) و گرد و غبار یک مسئله زیست محیطی مهم است. فرآیند احتراق در دمای بالا باعث تولید NOx می شود در حالی که وجود گوگرد در سوخت یا مواد اولیه منجر به تولید SOx می گردد. انتشار گرد و غبار نیز از خروجی کوره و سیستم پیش گرمکن رخ می دهد. رعایت استانداردهای زیست محیطی نیازمند استفاده از تجهیزات کنترل آلودگی مانند سیستم های کاهش NOx (مانند SNCR یا SCR) سیستم های حذف SOx و فیلترهای پیشرفته (مانند فیلترهای کیسه ای یا الکترواستاتیکی) است.
نوسانات دما در داخل کوره نیز می تواند بر کیفیت کلینکر و پایداری فرآیند تأثیر بگذارد. حفظ یک پروفیل دمایی پایدار در طول کوره برای اطمینان از کامل شدن واکنش های شیمیایی و تشکیل فازهای کلینکر با نسبت های مطلوب ضروری است. نوسانات دما می تواند ناشی از تغییرات در دبی خوراک دبی سوخت دبی هوای احتراق یا مشکلات در سیستم کنترل باشد.
تشکیل حلقه های کلینکر
تشکیل حلقه های کلینکر در کوره دوار یکی از مشکلات عملیاتی مکرر است که می تواند به سرعت ظرفیت تولید را کاهش داده و نیاز به توقف های اضطراری برای پاکسازی داشته باشد. حلقه ها معمولاً در مناطق خاصی از کوره مانند دهانه خروجی پیش گرمکن (در کوره های مجهز به پیش گرمکن) یا در میانه کوره تشکیل می شوند.
دلایل اصلی تشکیل حلقه ها عبارتند از:
- ترکیب شیمیایی نامناسب خوراک کوره: مقادیر بالای قلیاها (Na2O, K2O) سولفات ها کلریدها یا منیزیم اکسید در خوراک می تواند نقطه ذوب فازهای مایع را کاهش داده و باعث چسبندگی مواد به دیواره کوره شود.
- نوسانات دما و فرآیند پخت: تغییرات ناگهانی در دمای کوره یا شعله می تواند باعث ذوب شدن بیش از حد مواد و چسبیدن آن ها شود. پخت ناکافی یا بیش از حد نیز می تواند در تشکیل حلقه ها نقش داشته باشد.
- نوع و کیفیت سوخت: برخی سوخت ها به ویژه سوخت های جایگزین با ترکیب ناهمگن می توانند باعث ایجاد مشکلات در شعله و تشکیل رسوبات شوند.
- مشکلات مکانیکی کوره: مانند ناهمراستایی یا تاب برداشتن کوره می تواند باعث تمرکز مواد در یک نقطه و تسهیل تشکیل حلقه شود.
برای جلوگیری از تشکیل حلقه ها کنترل دقیق ترکیب شیمیایی خوراک کوره از طریق ترکیب مناسب مواد اولیه (Blending) و استفاده از روش های آنالیز آنلاین (مانند آنالیزور XRF روی خط) برای پایش ترکیب خوراک ورودی به کوره حیاتی است. استفاده از افزودنی های مناسب در خوراک کوره مانند افزودنی های معدنی که نقطه ذوب فاز مایع را کنترل می کنند یا افزودنی های شیمیایی که خواص چسبندگی را کاهش می دهند می تواند مؤثر باشد.
کنترل دقیق فرآیند احتراق و حفظ یک پروفیل دمایی پایدار در کوره از طریق تنظیم دقیق دبی سوخت هوای اولیه و ثانویه و سرعت چرخش کوره نیز بسیار مهم است. پایش مداوم وضعیت داخلی کوره با استفاده از دوربین های حرارتی و ابزارهای پایش آنلاین می تواند به شناسایی زودهنگام نشانه های تشکیل حلقه و انجام اقدامات اصلاحی قبل از جدی شدن مشکل کمک کند.
مشکلات در مرحله آسیاب سیمان
مرحله نهایی در فرآیند تولید سیمان آسیاب کردن کلینکر خروجی از کوره به همراه مقادیر مشخصی از گچ (برای کنترل زمان گیرش) و در برخی موارد مواد افزودنی مانند پوزولان ها سرباره کوره بلند یا خاکستر بادی است. هدف از این مرحله رسیدن به دانه بندی بسیار ریز و سطح مخصوص بالا در محصول نهایی (سیمان) است که برای واکنش با آب و کسب مقاومت ضروری است. این مرحله نیز چالش های فنی و عملیاتی خاص خود را دارد.
یکی از مهمترین مشکلات سایش شدید اجزای داخلی آسیاب های سیمان است. کلینکر ماده ای بسیار سخت و ساینده است و آسیاب کردن آن باعث فرسایش سریع لاینرها و گلوله ها در آسیاب های گلوله ای یا غلطک ها و سگمنت ها در آسیاب های عمودی می شود. سایش باعث کاهش راندمان آسیاب افت کیفیت محصول (مانند تغییر در توزیع دانه بندی) و نیاز به تعویض مکرر قطعات پرهزینه می شود.
تولید ذرات نامناسب یکی دیگر از مشکلات بالقوه است. سیمان باید دارای توزیع دانه بندی مشخصی باشد؛ نه خیلی درشت و نه خیلی ریز. ذرات خیلی درشت به طور کامل با آب واکنش نمی دهند و در کسب مقاومت اولیه و نهایی سیمان مشکل ایجاد می کنند. ذرات خیلی ریز نیز می توانند باعث گیرش سریع و مشکلات پایداری شوند. کنترل دقیق فرآیند آسیاب و استفاده از سپراتورهای (جداکننده های) با راندمان بالا برای جداسازی ذرات ریزتر و بازگرداندن ذرات درشت به آسیاب برای دستیابی به توزیع دانه بندی مطلوب ضروری است.
افزایش دما در داخل آسیاب سیمان نیز یک مشکل رایج است. فرآیند آسیاب کردن به ویژه در آسیاب های گلوله ای انرژی زیادی را به صورت حرارت آزاد می کند. افزایش بیش از حد دما در آسیاب می تواند باعث دهیدراته شدن جزئی گچ شود که این مسئله بر خواص گیرش سیمان تأثیر منفی می گذارد. کنترل دما از طریق تزریق آب به داخل آسیاب یا استفاده از سیستم های خنک کننده خارجی برای بدنه آسیاب امری ضروری است.
مصرف انرژی در مرحله آسیاب سیمان نیز قابل توجه است. این مرحله معمولاً پس از پخت بیشترین سهم را در مصرف انرژی الکتریکی کل کارخانه دارد. بهینه سازی فرآیند آسیاب استفاده از تکنولوژی های نوین آسیاب (مانند آسیاب های عمودی یا High Pressure Grinding Rolls – HPGR) به جای آسیاب های گلوله ای سنتی در ظرفیت های بالا و کنترل دقیق پارامترهای عملیاتی می تواند به کاهش مصرف انرژی کمک کند.
سایش آسیاب ها
سایش آسیاب های سیمان یک پدیده اجتناب ناپذیر است اما مدیریت و کاهش آن برای حفظ راندمان تولید و کاهش هزینه ها اهمیت حیاتی دارد. سایش ناشی از اصطکاک و ضربه بین مواد سخت (کلینکر و مواد افزودنی) و اجزای فلزی یا سرامیکی داخلی آسیاب است.
عوامل مؤثر بر شدت سایش عبارتند از:
- سختی و سایندگی مواد: کلینکر با سختی بالا و وجود ذرات کوارتز در مواد افزودنی اصلی ترین عامل سایش هستند.
- نوع آسیاب و طراحی داخلی آن: طراحی لاینرها و نوع گلوله ها (در آسیاب گلوله ای) یا جنس و شکل غلطک ها و سگمنت ها (در آسیاب عمودی) بر الگوی سایش تأثیر می گذارد.
- شرایط عملیاتی: سرعت چرخش آسیاب میزان پرشدگی (در آسیاب گلوله ای) فشار غلطک ها (در آسیاب عمودی) و دبی مواد ورودی همگی بر شدت سایش مؤثرند.
- جنس قطعات داخلی: مقاومت به سایش مواد به کار رفته در ساخت لاینرها گلوله ها یا غلطک ها نقش تعیین کننده ای دارد. استفاده از فولادهای منگنزی فولادهای کروم بالا یا مواد سرامیکی با مقاومت به سایش بالا می تواند عمر مفید قطعات را افزایش دهد.
راهکارهای کاهش سایش شامل استفاده از مواد مقاوم در برابر سایش با آلیاژهای ویژه برای ساخت لاینرها گلوله ها غلطک ها و سگمنت ها است. بهینه سازی فرآیند آسیاب از طریق تنظیم پارامترهای عملیاتی برای کاهش نیروهای ساینده و ضربه ای مانند کنترل دبی مواد ورودی و سرعت چرخش نیز می تواند مؤثر باشد. استفاده از تکنولوژی های نوین آسیاب مانند HPGR که اساس عملکرد آن ها بر فشار بالا است نه ضربه و سایش گلوله ها می تواند به طور قابل توجهی سایش را کاهش دهد.
مشکلات مرتبط با کیفیت سیمان تولیدی
کیفیت سیمان تولیدی که در نهایت تعیین کننده عملکرد سازه های بتنی است باید با استانداردهای ملی و بین المللی مطابقت داشته باشد. مشکلات کیفی در سیمان می توانند منجر به عواقب جدی در پروژه های ساختمانی شوند. کنترل کیفیت در تمام مراحل تولید برای اطمینان از رسیدن به محصول نهایی با خواص مطلوب ضروری است.
یکی از مشکلات اساسی مقاومت پایین سیمان است. مقاومت فشاری و خمشی سیمان پس از گیرش و سخت شدن مهمترین شاخص کیفیت آن است. مقاومت پایین می تواند ناشی از عوامل متعددی در فرآیند تولید باشد:
- ترکیب شیمیایی نامناسب کلینکر: نسبت های نادرست فازهای کلینکر (C3S, C2S, C3A, C4AF) به دلیل ترکیب شیمیایی نامتعادل خوراک کوره یا فرآیند پخت نامناسب می تواند مقاومت را کاهش دهد. به عنوان مثال نسبت پایین C3S (تری کلسیم سیلیکات) که عامل اصلی کسب مقاومت اولیه و نهایی است منجر به سیمانی با مقاومت کمتر می شود.
- پخت ناکافی کلینکر: اگر دمای پخت در کوره به اندازه کافی بالا نباشد یا زمان ماند مواد در منطقه پخت کوتاه باشد واکنش های کلینکرزاسیون به طور کامل انجام نمی شوند و کلینکر حاصل دارای مقادیر زیادی آهک آزاد (Free Lime) یا بلورهای C2S بزرگ می شود که هر دو بر مقاومت و پایداری سیمان تأثیر منفی دارند.
- آسیاب نامناسب سیمان: اگر سیمان به اندازه کافی ریز نباشد (سطح مخصوص پایین) هیدراسیون به طور کامل انجام نمی شود و مقاومت کاهش می یابد. توزیع دانه بندی نامناسب نیز می تواند بر خواص سیمان تأثیر بگذارد.
- کیفیت پایین مواد افزودنی: کیفیت و نوع گچ و سایر افزودنی ها (مانند پوزولان ها) نیز بر خواص سیمان از جمله مقاومت تأثیر می گذارد.
گیرش نامناسب (خیلی سریع یا خیلی کند) یکی دیگر از مشکلات کیفی است. گیرش سریع می تواند ناشی از مقادیر بالای C3A فعال یا کمبود گچ باشد در حالی که گیرش کند ممکن است به دلیل کمبود C3A یا وجود مواد بازدارنده در مواد اولیه یا افزودنی ها رخ دهد. ترک خوردگی در بتن سخت شده نیز می تواند به مشکلات کیفی سیمان مرتبط باشد مانند وجود مقادیر بالای آهک آزاد یا منیزیم اکسید که باعث انبساط تأخیری می شوند.
تغییرات شیمیایی نامطلوب در سیمان مانند واکنش قلیایی سنگدانه (ASR) یا حمله سولفات ها نیز به ترکیب شیمیایی سیمان مربوط می شود. مقادیر بالای قلیاها در سیمان می تواند باعث ASR شود در حالی که مقاومت به حمله سولفات ها به ترکیب شیمیایی کلینکر و مقدار C3A بستگی دارد.
مقاومت پایین سیمان
مقاومت پایین سیمان مشکلی جدی است که می تواند اعتماد به محصول و ایمنی سازه ها را تحت تأثیر قرار دهد. همانطور که اشاره شد این مشکل می تواند ریشه در مراحل مختلف تولید داشته باشد. برای رفع این مشکل لازم است یک سیستم کنترل کیفیت جامع و مؤثر در تمام مراحل تولید پیاده سازی شود.
راهکارهای کلیدی برای افزایش و تضمین مقاومت سیمان عبارتند از:
- کنترل دقیق ترکیب مواد اولیه: اطمینان از نسبت های صحیح سنگ آهک خاک رس و سایر مواد اولیه برای دستیابی به مدول های شیمیایی مطلوب در خوراک کوره (مانند مدول سیلیکات مدول آلومینات و نسبت آهک). استفاده از سیستم های ترکیب مواد اولیه (Blending Bed یا Silo Blending) برای یکنواخت کردن ترکیب شیمیایی خوراک.
- بهینه سازی فرآیند پخت کلینکر: حفظ دمای پخت مناسب و پایدار در کوره برای اطمینان از تکمیل واکنش های کلینکرزاسیون و تشکیل فازهای کلینکر با نسبت های بهینه به ویژه C3S. کنترل میزان آهک آزاد در کلینکر خروجی.
- کنترل دقیق فرآیند آسیاب سیمان: دستیابی به سطح مخصوص (Fineness) و توزیع دانه بندی مطلوب در سیمان نهایی. استفاده از سپراتورهای با راندمان بالا برای جداسازی دقیق ذرات. تنظیم پارامترهای آسیاب برای بهینه سازی فرآیند.
- استفاده از مواد افزودنی با کیفیت: اطمینان از کیفیت و خلوص گچ و سایر مواد افزودنی مورد استفاده. تنظیم دقیق نسبت گچ به کلینکر برای کنترل زمان گیرش و تأثیر بر مقاومت.
- آزمایش های کیفی منظم: انجام آزمایش های شیمیایی و فیزیکی (مانند مقاومت فشاری زمان گیرش پایداری حجمی) بر روی نمونه های سیمان تولیدی در فواصل زمانی منظم و مقایسه نتایج با استانداردهای مربوطه. استفاده از آزمایشگاه مجهز و پرسنل آموزش دیده برای انجام دقیق آزمایش ها.
راهکارهای جامع برای بهبود فرآیند تولید سیمان
بهبود فرآیند تولید سیمان و غلبه بر مشکلات رایج نیازمند یک رویکرد جامع و چندوجهی است که تمام مراحل زنجیره تولید را در بر گیرد. صرف تمرکز بر یک مشکل خاص بدون توجه به ارتباط آن با سایر بخش ها معمولاً نتایج پایداری به همراه نخواهد داشت. این رویکرد جامع شامل عناصر کلیدی زیر است:
- بهینه سازی فرآیند: این شامل مطالعه و تحلیل دقیق پارامترهای عملیاتی در هر مرحله (از استخراج تا آسیاب نهایی) و شناسایی نقاط ضعف و فرصت های بهبود است. بهینه سازی می تواند شامل تنظیم نسبت مواد اولیه کنترل دقیق دمای کوره بهینه سازی مصرف سوخت تنظیم پارامترهای آسیاب و بهبود سیستم های حمل و نقل مواد باشد.
- استفاده از تکنولوژی های نوین: صنعت سیمان به طور مداوم در حال توسعه و پذیرش تکنولوژی های جدید برای افزایش راندمان کاهش هزینه ها بهبود کیفیت و کاهش اثرات زیست محیطی است. این تکنولوژی ها شامل سنگ شکن ها و آسیاب های پیشرفته تر سیستم های پیش گرمکن و کلسینر با راندمان حرارتی بالاتر استفاده از سوخت های جایگزین سیستم های کنترل آلودگی هوا پیشرفته و سیستم های اتوماسیون و کنترل هوشمند است.
- آموزش و توانمندسازی پرسنل: اپراتورها تکنسین ها و مهندسان شاغل در کارخانه سیمان باید دارای دانش فنی به روز و مهارت های لازم برای کار با تجهیزات پیشرفته پایش فرآیند تشخیص مشکلات و انجام اقدامات اصلاحی باشند. برنامه های آموزشی منظم و مستمر برای ارتقاء دانش و مهارت های پرسنل ضروری است.
- استقرار سیستم های کنترل کیفیت جامع (TQM): کنترل کیفیت نباید تنها محدود به آزمایش محصول نهایی باشد. یک سیستم کنترل کیفیت مؤثر باید از لحظه استخراج مواد اولیه آغاز شده و تمام مراحل فرآیند را شامل شود. این شامل نمونه برداری و آنالیز منظم مواد اولیه خوراک کوره کلینکر و سیمان نهایی استفاده از ابزارهای آماری برای تحلیل داده ها و شناسایی روندهای نامطلوب و پیاده سازی اقدامات اصلاحی پیشگیرانه است.
- مدیریت نگهداری و تعمیرات (Maintenance Management): نگهداری منظم و پیشگیرانه تجهیزات برای جلوگیری از خرابی های ناگهانی کاهش توقفات ناخواسته و افزایش عمر مفید تجهیزات حیاتی است. پیاده سازی سیستم های نگهداری مبتنی بر پایش وضعیت (Condition Monitoring) می تواند به پیش بینی زمان خرابی تجهیزات و برنامه ریزی مؤثر تعمیرات کمک کند.
نقش اتوماسیون در کاهش مشکلات تولید سیمان
اتوماسیون صنعتی و استفاده از سیستم های کنترل هوشمند نقش فزاینده ای در بهبود فرآیند تولید سیمان و کاهش بسیاری از مشکلات رایج ایفا می کنند. این سیستم ها با جمع آوری داده ها از سنسورهای متعدد در طول خط تولید تحلیل آن ها و اعمال تنظیمات لازم بر روی تجهیزات امکان پایش و کنترل دقیق و بلادرنگ فرآیند را فراهم می آورند.
مزایای استفاده از اتوماسیون در صنعت سیمان شامل موارد زیر است:
- افزایش پایداری فرآیند: سیستم های کنترل خودکار می توانند پارامترهای کلیدی مانند دبی مواد ورودی دمای کوره دبی سوخت و دبی هوا را با دقت بسیار بالایی کنترل کنند. این پایداری باعث کاهش نوسانات در فرآیند و در نتیجه کاهش مشکلاتی مانند تشکیل حلقه های کوره نوسانات دما و کیفیت غیریکنواخت کلینکر می شود.
- بهینه سازی مصرف انرژی: سیستم های کنترل پیشرفته (مانند سیستم های کنترل بهینه یا Model Predictive Control – MPC) می توانند با تحلیل پیچیده داده ها بهترین ترکیب پارامترها را برای دستیابی به حداکثر راندمان انرژی پیدا کنند. این امر به ویژه در کاهش مصرف سوخت کوره و انرژی الکتریکی آسیاب ها مؤثر است.
- بهبود کیفیت محصول: با کنترل دقیق ترکیب شیمیایی خوراک کوره (از طریق سیستم های اختلاط خودکار و آنالیز آنلاین) و پایش لحظه ای پارامترهای پخت و آسیاب اتوماسیون به تولید کلینکر و سیمانی با کیفیت یکنواخت تر و مطابق با استانداردها کمک می کند.
- کاهش خطاهای انسانی: بسیاری از مشکلات در فرآیندهای پیچیده ناشی از خطاهای اپراتوری یا تأخیر در واکنش به تغییرات فرآیندی هستند. سیستم های اتوماسیون با واکنش سریع و دقیق این خطاهای انسانی را به حداقل می رسانند.
- پیش بینی و تشخیص زودهنگام مشکلات: سیستم های اتوماسیون پیشرفته با استفاده از الگوریتم های تحلیلی و یادگیری ماشین می توانند الگوهای غیرعادی در داده های فرآیندی را شناسایی کرده و نشانه های اولیه بروز مشکلاتی مانند گرفتگی آسیاب ها یا تشکیل حلقه ها را قبل از جدی شدن آن ها پیش بینی کنند. این امر امکان انجام اقدامات پیشگیرانه را فراهم می آورد.
- افزایش ایمنی: اتوماسیون با کاهش نیاز به حضور پرسنل در مناطق خطرناک و کنترل دقیق تر فرآیندها به افزایش ایمنی در کارخانه کمک می کند.
پیاده سازی موفق سیستم های اتوماسیون نیازمند سرمایه گذاری اولیه زیرساخت های مناسب و پرسنل آموزش دیده برای بهره برداری و نگهداری از این سیستم ها است. اما منافع بلندمدت آن از نظر افزایش راندمان کاهش هزینه ها بهبود کیفیت و پایداری تولید سرمایه گذاری را توجیه می کند.
FAQ
چگونه می توان از تشکیل حلقه های کلینکر در کوره جلوگیری کرد؟
برای جلوگیری از حلقه های کلینکر ترکیب شیمیایی خوراک کوره را دقیق کنترل کنید دمای پخت را پایدار نگه دارید از سوخت مناسب استفاده کنید و در صورت لزوم از افزودنی های ضد حلقه بهره ببرید.
چه راهکارهایی برای کاهش مصرف انرژی در فرآیند تولید سیمان وجود دارد؟
راهکارها شامل بهینه سازی کوره و پیش گرمکن استفاده از سوخت های جایگزین بهبود راندمان آسیاب ها (مانند استفاده از VRM یا HPGR) و پیاده سازی سیستم های اتوماسیون پیشرفته است.
چگونه می توان از سایش آسیاب ها در مرحله آسیاب سیمان جلوگیری کرد؟
برای کاهش سایش آسیاب ها از مواد مقاوم در برابر سایش با آلیاژهای خاص در ساخت قطعات استفاده کنید پارامترهای عملیاتی آسیاب را بهینه کنید و تکنولوژی های نوین آسیاب با سایش کمتر را به کار بگیرید.
مهمترین عوامل موثر بر کیفیت سیمان تولیدی کدامند؟
کیفیت سیمان به ترکیب شیمیایی مواد اولیه کنترل دقیق فرآیند پخت کلینکر (دما و زمان) کیفیت و فرآیند آسیاب نهایی سیمان و نوع و نسبت مواد افزودنی بستگی دارد.
چگونه می توان آلودگی هوا ناشی از تولید سیمان را کاهش داد؟
کاهش آلودگی هوا با استفاده از فیلترهای کیسه ای و الکترواستاتیکی برای کنترل گرد و غبار سیستم های کاهش NOx (مانند SNCR) و سیستم های حذف SOx امکان پذیر است.
آیا شما به دنبال کسب اطلاعات بیشتر در مورد "مشکلات رایج در تولید سیمان و راه حل ها" هستید؟ با کلیک بر روی اقتصادی, کسب و کار ایرانی، آیا به دنبال موضوعات مشابهی هستید؟ برای کشف محتواهای بیشتر، از منوی جستجو استفاده کنید. همچنین، ممکن است در این دسته بندی، سریال ها، فیلم ها، کتاب ها و مقالات مفیدی نیز برای شما قرار داشته باشند. بنابراین، همین حالا برای کشف دنیای جذاب و گسترده ی محتواهای مرتبط با "مشکلات رایج در تولید سیمان و راه حل ها"، کلیک کنید.